“The Toyota Way” by Jeffrey K. Liker explores Toyota’s management principles and practices. It reveals the secrets behind Toyota’s success.
Jeffrey K. Liker’s “The Toyota Way” provides deep insights into Toyota’s renowned management philosophy. This audiobook explains the 14 principles that form the backbone of Toyota’s exceptional performance and quality. It details how these principles focus on long-term results, even at the expense of short-term financial goals.
The book emphasizes continuous improvement and respect for people as core values. Managers and business leaders can apply these principles to enhance their operations. Liker’s work is essential for anyone looking to understand the mechanisms behind Toyota’s success and how to implement similar strategies in their own organizations.
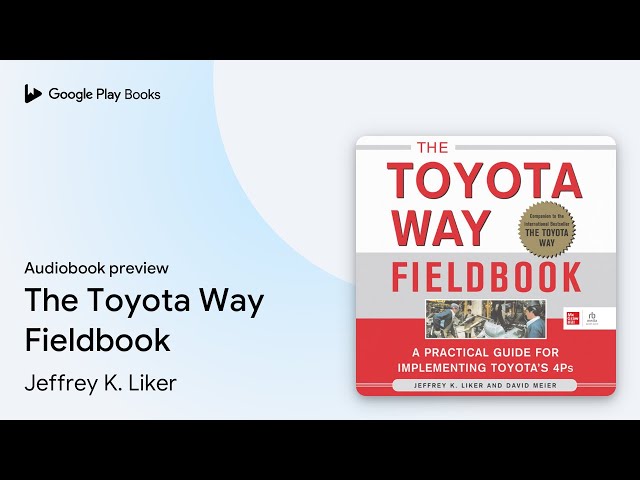
The Essence Of The Toyota Way
The Toyota Way focuses on continuous improvement and respect for people. It encourages employees to always seek better ways. Respect for people means valuing every team member. Both principles drive Toyota’s success.
- Challenge: Always have a long-term vision.
- Kaizen: Continuously improve operations.
- Genchi Genbutsu: Go to the source to find facts.
- Respect: Respect others and strive for mutual trust.
- Teamwork: Stimulate personal and professional growth.
Lean Manufacturing And Continuous Improvement
The Toyota Way teaches us about lean manufacturing. It focuses on improving processes every day. Workers aim for operational excellence. They reduce mistakes and improve efficiency. This method encourages teamwork. Everyone has a role in making things better. Small changes make a big impact.
Kaizen is a core part of The Toyota Way. It means continuous improvement. Workers identify and eliminate waste. Waste can be time, materials, or effort. Teams brainstorm solutions. They quickly test and implement changes. This creates a cycle of constant improvement. It keeps the production process efficient and effective.
Respect For People
Respect for people means valuing every person. Each worker is important. Everyone’s opinion matters. A respectful culture encourages open communication. People feel safe to share ideas. This culture helps in solving problems quickly. It promotes a happy workplace.
Empowerment means giving workers the power to make decisions. It builds confidence in employees. Teamwork is working together towards a common goal. Teams can solve problems faster. Collaboration and trust are key in teams. Empowered teams are more productive. People enjoy their work more.
Long-term Thinking
Jeffrey K. Liker’s audiobook, “The Toyota Way,” emphasizes long-term thinking for sustainable success. This approach fosters continuous improvement and innovation.
Balancing Short-term Gains With Future Vision
Companies often focus on short-term gains. This can lead to missing future opportunities. Long-term thinking helps balance these goals. Toyota is a great example. They focus on what will happen in the future. This way, they can plan better. Short-term wins are important too. But, without a future vision, they might not last.
Sustaining Growth And Innovation
Sustaining growth requires ongoing efforts. Innovation must be constant. Toyota invests in both areas. They do not just aim for quick success. They also plan for long-term success. This balance helps them stay strong. It keeps them ahead in the market.
The 14 Principles Of The Toyota Way
Jeffrey K. Liker explains the core ideas of Toyota’s success. The 14 principles guide the company. They focus on continuous improvement and respect for people. Each principle plays a vital role.
One principle is long-term thinking. This means making decisions with the future in mind. Another is to solve problems at the root. This helps prevent issues from happening again. Standardizing tasks ensures quality and efficiency.
Employee involvement is also key. Workers suggest improvements. This makes them feel valued. Building a culture of teamwork is essential. Everyone works together toward common goals. Learning from mistakes helps the company grow stronger.
Many companies use Toyota’s principles. They find them very effective. One example is a car manufacturing plant. Workers there follow standardized tasks. This reduces errors and boosts productivity. Another example is a hospital. Staff members suggest improvements. This leads to better patient care.
A tech company also benefits. They focus on long-term thinking. This helps them stay ahead in the market. Another case is a retail store. They practice continuous improvement. This keeps their customers happy. These real-world examples show how powerful these principles are.
Problem-solving The Toyota Way
The 5 Whys method helps find the root cause of a problem. You start by asking “Why?” five times. Each answer leads to the next “Why?”. This simple method digs deep into issues. It uncovers hidden problems. This technique helps solve problems effectively. Teams use it to find real solutions. Everyone can understand and use the 5 Whys. It is easy and powerful.
Standardized tasks ensure quality and efficiency. Everyone follows the same steps. This reduces mistakes. Workers can then focus on solving new problems. Creativity comes into play here. They think of new ways to improve tasks. This balance of standardization and creativity drives success. It keeps operations smooth and innovative. The Toyota Way shows how to achieve this balance.
Adapting The Toyota Way In Different Cultures
Many companies face cultural barriers. Employees may resist changes. Some cultures value hierarchy and seniority more. This conflicts with Toyota’s team-based approach. Language barriers can also be an issue. Communication becomes difficult. Training methods may need adjustments. Local laws and regulations differ. This affects process standardization. Adapting to local markets is crucial. Flexibility and understanding are key.
Toyota’s principles have been adopted globally. A notable success is in the United States. Toyota’s plant in Kentucky is very efficient. They follow the Toyota Production System. In Europe, companies have also succeeded. For example, a plant in the United Kingdom achieved record production. Brazil has also seen improvements. A factory there increased productivity by 20%. These examples show the universal value of Toyota’s methods.
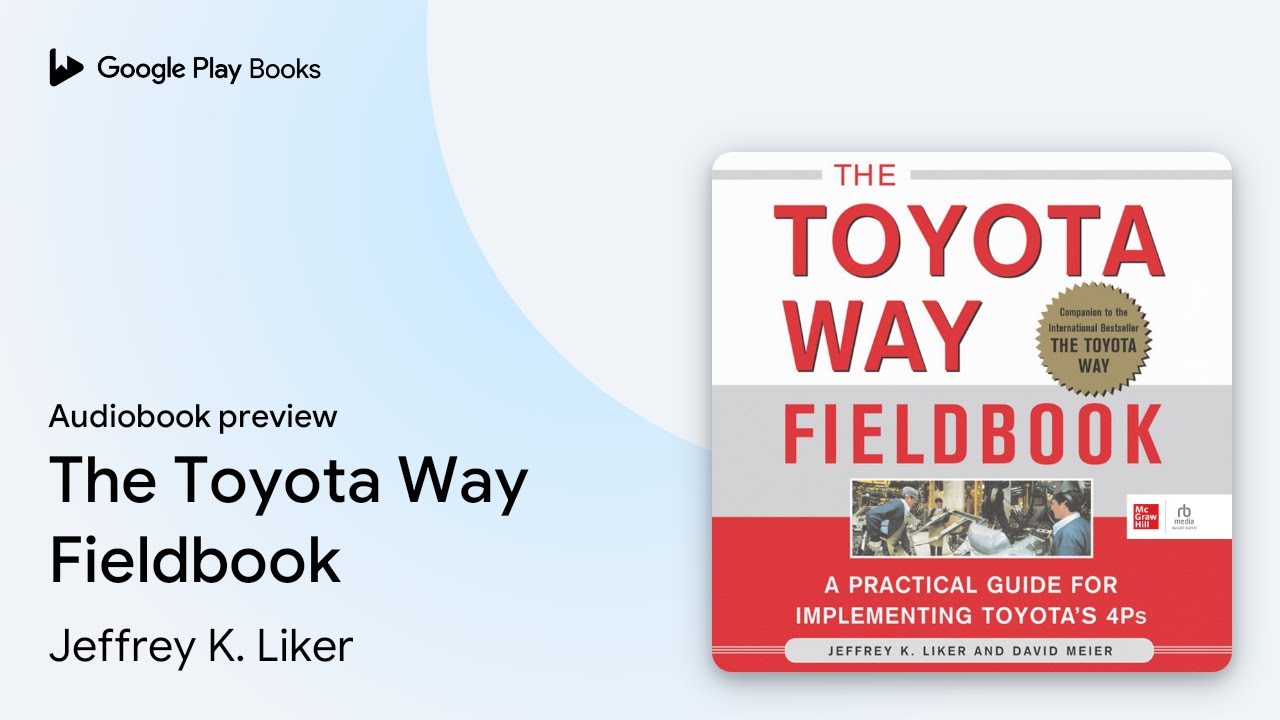
Impact On The Automotive Industry And Beyond
The Toyota Way has changed global manufacturing. Many companies have copied Toyota’s methods. These methods focus on efficiency and quality. Factories around the world use these techniques. This has improved their productivity and customer satisfaction. The book explains how Toyota became a leader in the car industry.
Other industries have also learned from Toyota. Hospitals use Toyota’s methods to improve patient care. Schools use them to enhance learning. Even restaurants have adopted these principles. The lessons from The Toyota Way are useful everywhere. Businesses can become better by following these ideas.
Criticisms And Limitations
Critics argue that The Toyota Way model is too rigid. They believe it does not fit all companies. Some say it is too focused on manufacturing. They argue it neglects other industries.
Others think the model is too complex. They find it hard to implement. Some believe it requires too much time and resources. These points highlight important limitations.
The Toyota Way may not work for every company. It is best suited for large organizations. Smaller companies might struggle to apply it. The principles are designed for long-term use.
Flexibility is key in business. Companies need to adapt the model to fit their needs. Some may need to modify the principles. Understanding these boundaries is crucial for success.
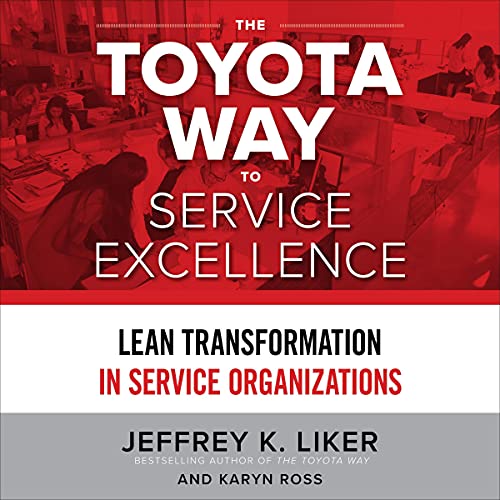
Future Of The Toyota Way
Automation and AI are changing the car industry. Toyota is using these tools to improve. Robots help in the factories. They do jobs that are hard for people. AI helps in making better cars. It helps in planning and testing. These changes make work faster and safer.
Toyota keeps its values strong. Even with new technology, it cares about people. The company trains workers to use new tools. People and machines work together. This balance keeps Toyota strong. They stay true to their way while growing with the world.
Conclusion
The Toyota Way audiobook by Jeffrey K. Liker offers invaluable insights into efficient business practices. This guide is essential for anyone aiming to improve operations. It provides practical steps to implement Toyota’s principles. Don’t miss this opportunity to enhance your understanding of lean management.
Listen to the audiobook and transform your approach today.